長期以來,國內建筑瓷磚的生產主要采用濕法球磨制粉技術,從原料到粉料,一般要經歷原料投放→加水(按比例往球磨機中加水)→對原料進行球磨(通過鋁球石將原料磨細,一般時間為12小時以上)→放入攪拌池→噴霧塔干燥(料液從塔頂噴出,干燥成品從底部排除,廢氣由風機排除)5個流程。在此過程中,原料經過加水,濕度達到35%,而后的噴霧塔干燥則通過高溫蒸發水分,把濕度降為7~8%,整個球磨工序耗時長,能耗大。
總體而言,濕法球磨制粉技術生產設備占地面積大,生產過程中消耗大量資源、能源,其中耗電量就占據了整個生產線電耗的1/3,更會造成廢氣、粉塵污染,為建陶行業的生產帶來巨大生產成本與環境壓力。而創新干法制粉工藝,從原料到粉料,則要經歷原料投放→干法破碎(精細研磨,減少顆粒尺寸和混合粉料)→原料均化(不同原料混合均化,使物料的化學成分均勻一致的過程)→干法造粒→粉料干燥、篩選(符合質量要求的陶瓷粉料)5個生產流程。
干法制粉技術將原材料水分增加到15%左右,干燥至7%,節能和節水的優勢極為明顯。
與濕法制粉相比,干法制粉完全消除了濕法造粒噴霧塔環節,減少了濕法工藝的“加水→蒸發”過程,直接節約用水70%以上,與之相應的是蒸發這些水的用電、用燃料及產生的排放等,還有濕法工藝中的大型設備球磨機與噴霧干燥塔及漿池等。
相對來說,干法制粉具有生產工藝簡單連續,所需設備少、占地少、投資少、產量大、生產效率高、節能減排,干法制粉工藝過程可以做成全過程封閉自動化系統,只用電不用任何燃料,做到零廢氣、零粉塵排放。據了解,以生產1噸陶瓷粉料為準,干法制粉比濕法制粉節能35%左右、節水70%左右、二氧化碳減排36%左右、節電12%左右,綜合能耗減少45%以上。
2014年4月24日,十二屆全國人大常委會第八次會議表決通過了《環保法修訂案》,新法將于2015年1月1日施行。與此同時,今年夏季以來,以廣東肇慶為代表的產區開始了對陶瓷企業環保的整治。
在此背景之下,一邊是政府對環保的高壓態勢,一邊則是陶瓷企業在傳統濕法工藝之下除塵、減排的目標幾乎難以實現的窘境。
或許,屬于中國建筑陶瓷產業干法制粉工藝的曙光就要來臨了。
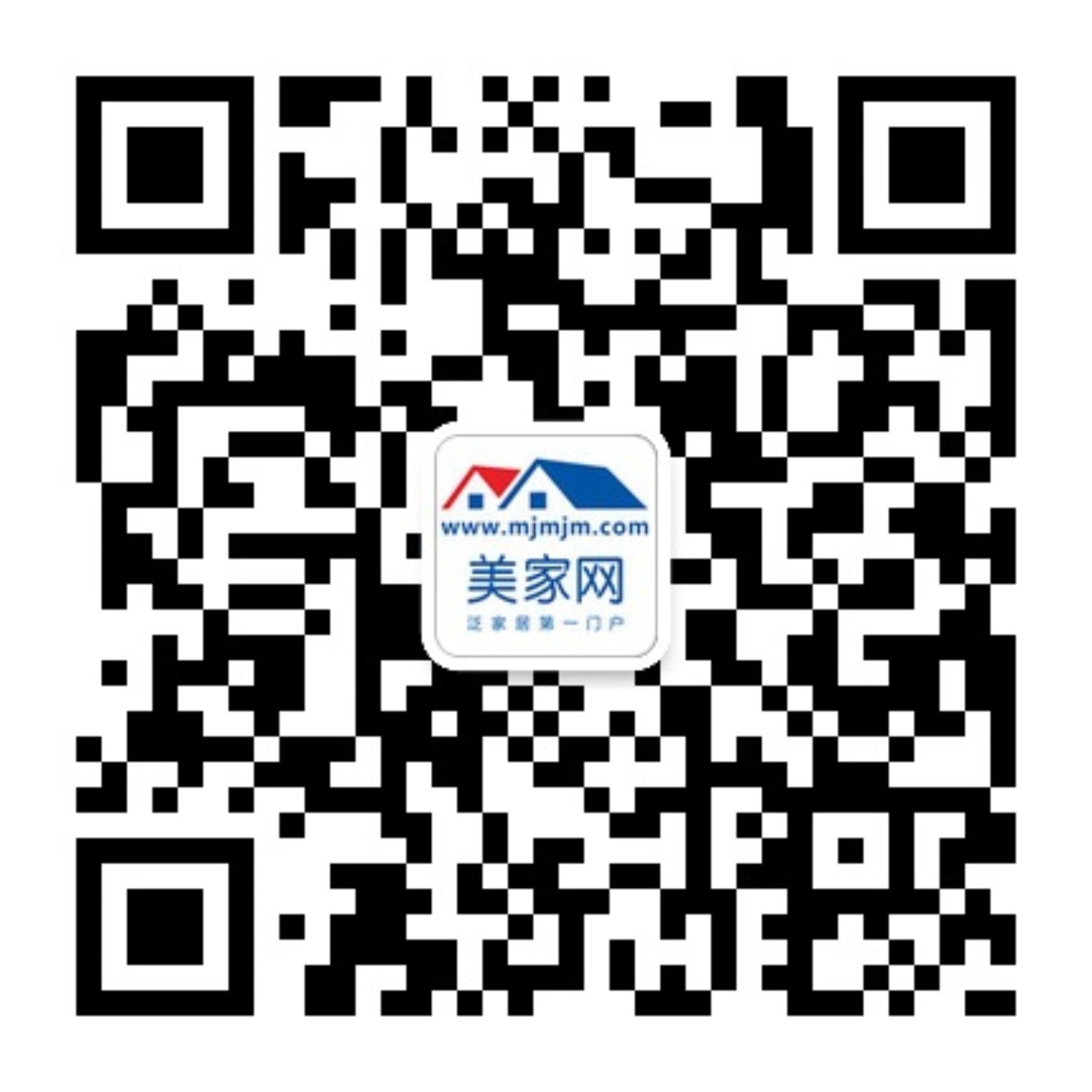